With this blog post on the release of the Direct Die Frame V2, we would like to provide an insight into production at Thermal Grizzly. We will show the individual production steps of the Ryzen Direct Die Frame V2 and also discuss quality control. This is carried out during operation so that we can react in real time to any problems that may arise. The new Ryzen Direct Die Frame V2 will be available in the next few weeks and will extend the compatibility of the DDF to include the Ryzen 7000X3D CPUs.
Incoming inspection and preparation of the aluminum plates
We manufacture the Direct Die Frames V2 (DDF) from aluminum plates with 7075 alloy. This alloy is often used in the production of aircraft parts as it is very resistant to material fatigue and also has good ductility and high strength. This high-quality aluminum alloy is also used for our contact frames and has the advantage that the frames, contact and direct-die, are practically torsion-free.
When the aluminum panels are delivered in dimensions of 70 cm long and 44 cm wide, the panels are first checked for visible notches or unevenness that could affect the milling process. The height of the panels is also checked to ensure that they are within the guaranteed tolerances. Before the DDF is actually produced, the panels are prepared for milling. To do this, holes for the fastening screws and dowel pins are drilled and chamfered on a Datron M8 on the vacuum table.
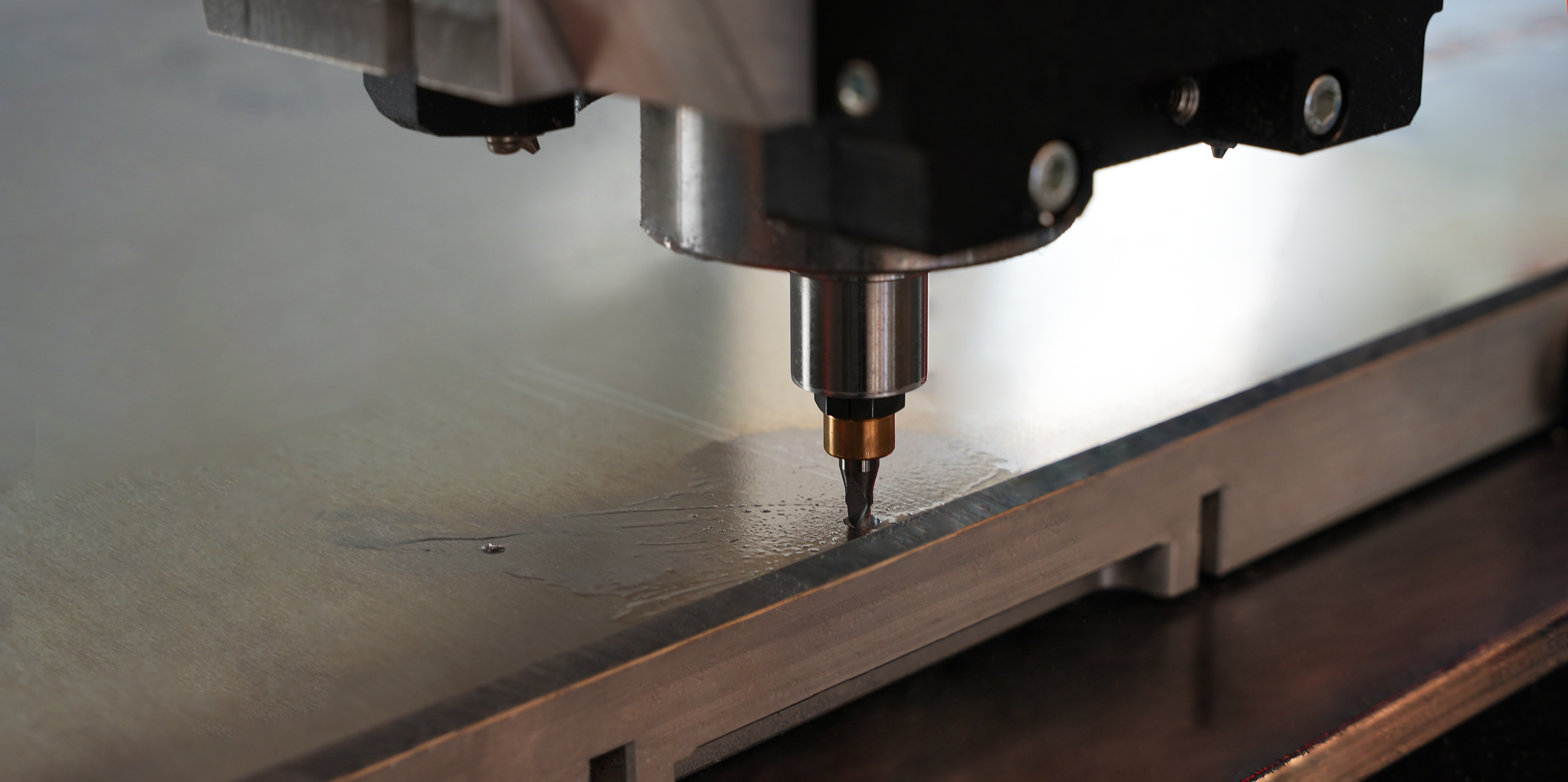
Milling the Direct-Die-Frames
The direct-die frames are milled in three steps, for which the aluminum plates are screwed together in one clamping. First, the top side is machined before the panel has to be turned for the second step. While the first step is carried out relatively quickly, the second step takes considerably longer, as this is where most of the processing takes place. In the third step, the individual direct-die frames are fixed to the clamping fixture with hold-down clamps so that they can be milled out of the panel.
We mill the DDFs on a Datron M10 Pro. The M10 Pro is a high-speed milling machine with an 8kW spindle and linear scales. The linear scales enable the CNC milling machine to achieve maximum precision in its movements. The 8kW spindle enables the M10 to carry out milling work on aluminum at a feed rate of 4,000 mm/min. The feed rate is the speed at which the tool is moved over the workpiece. The rotational speed of the spindle, i.e. the tool holder, is 34,000 rpm.
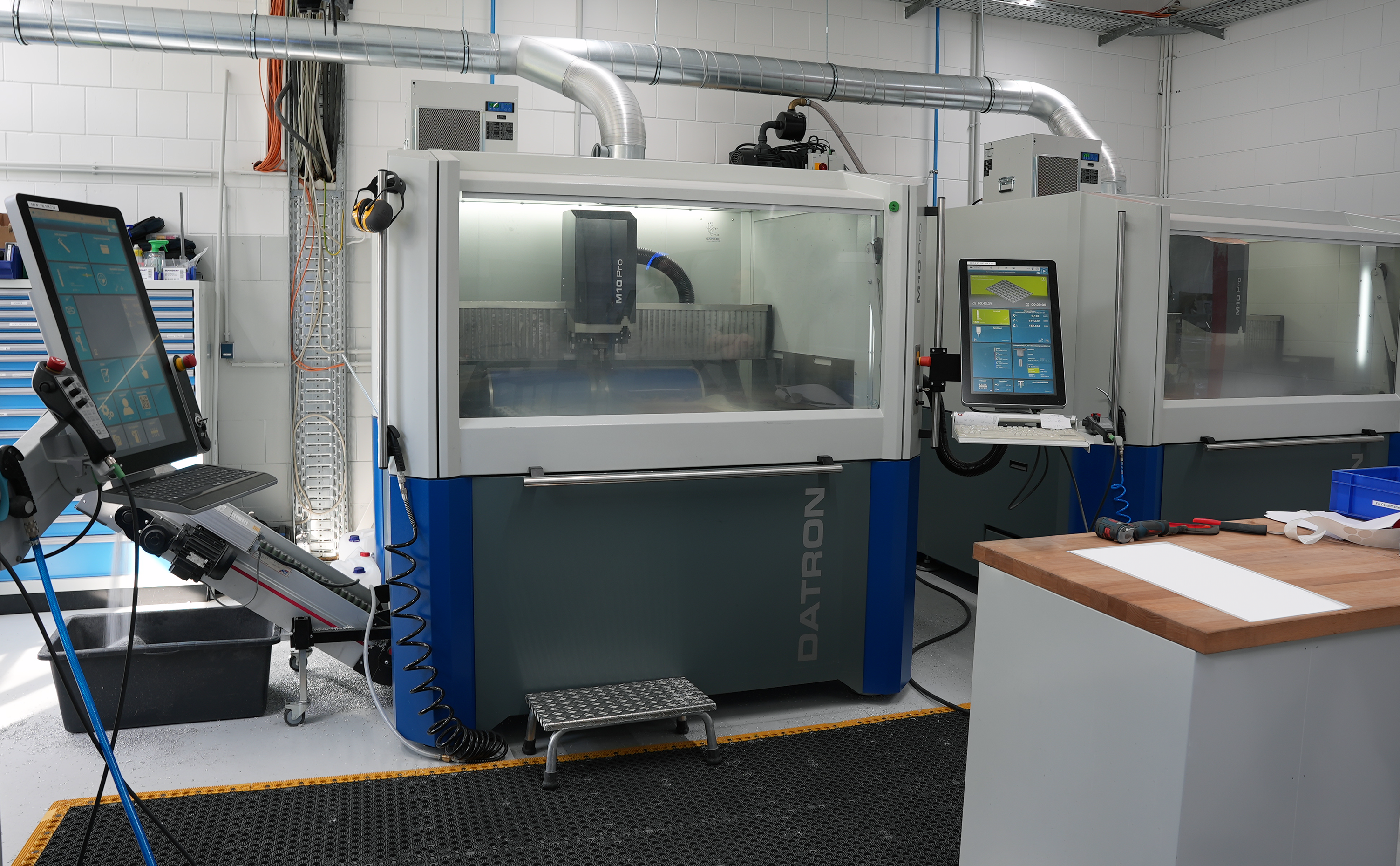
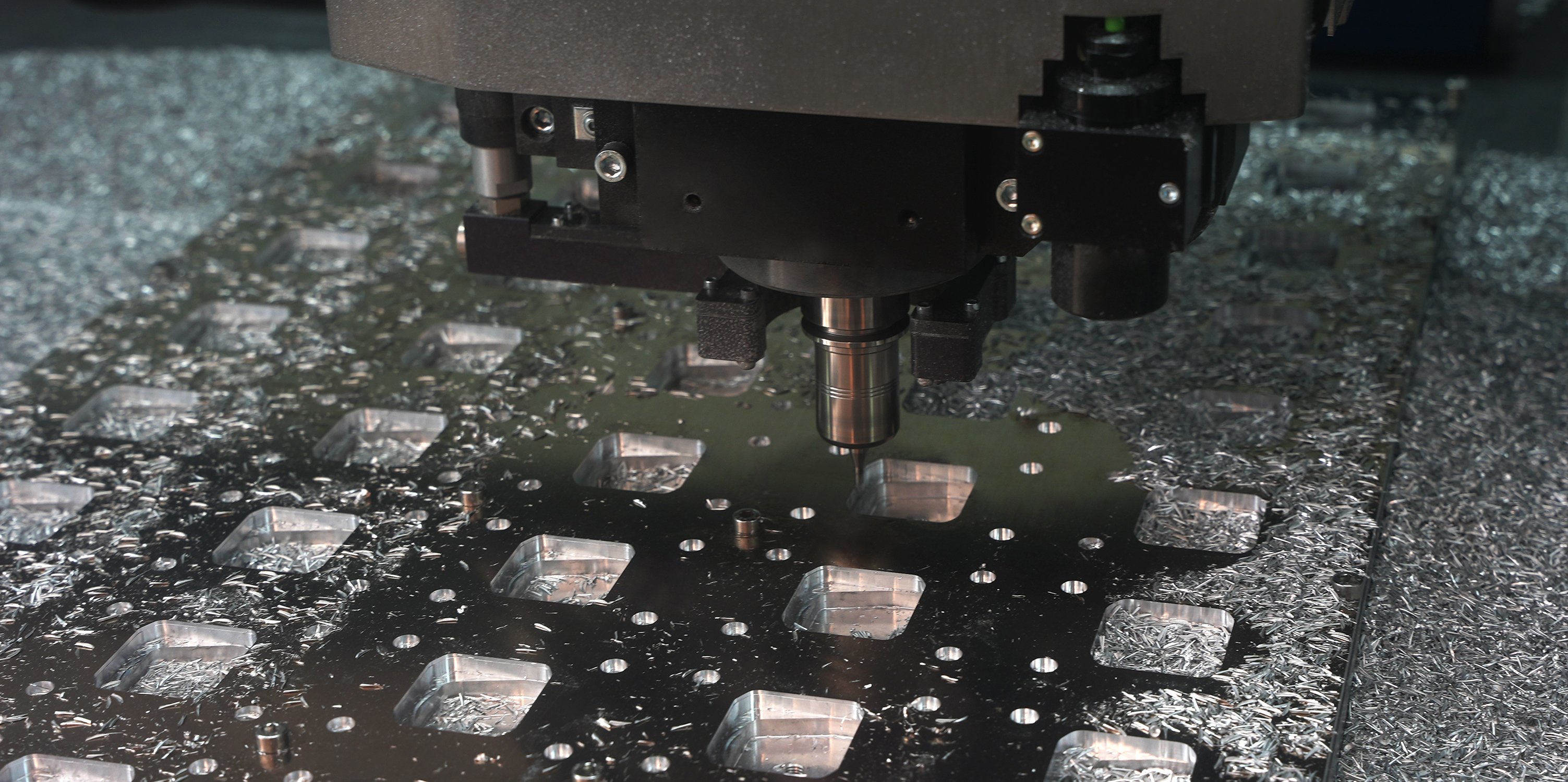
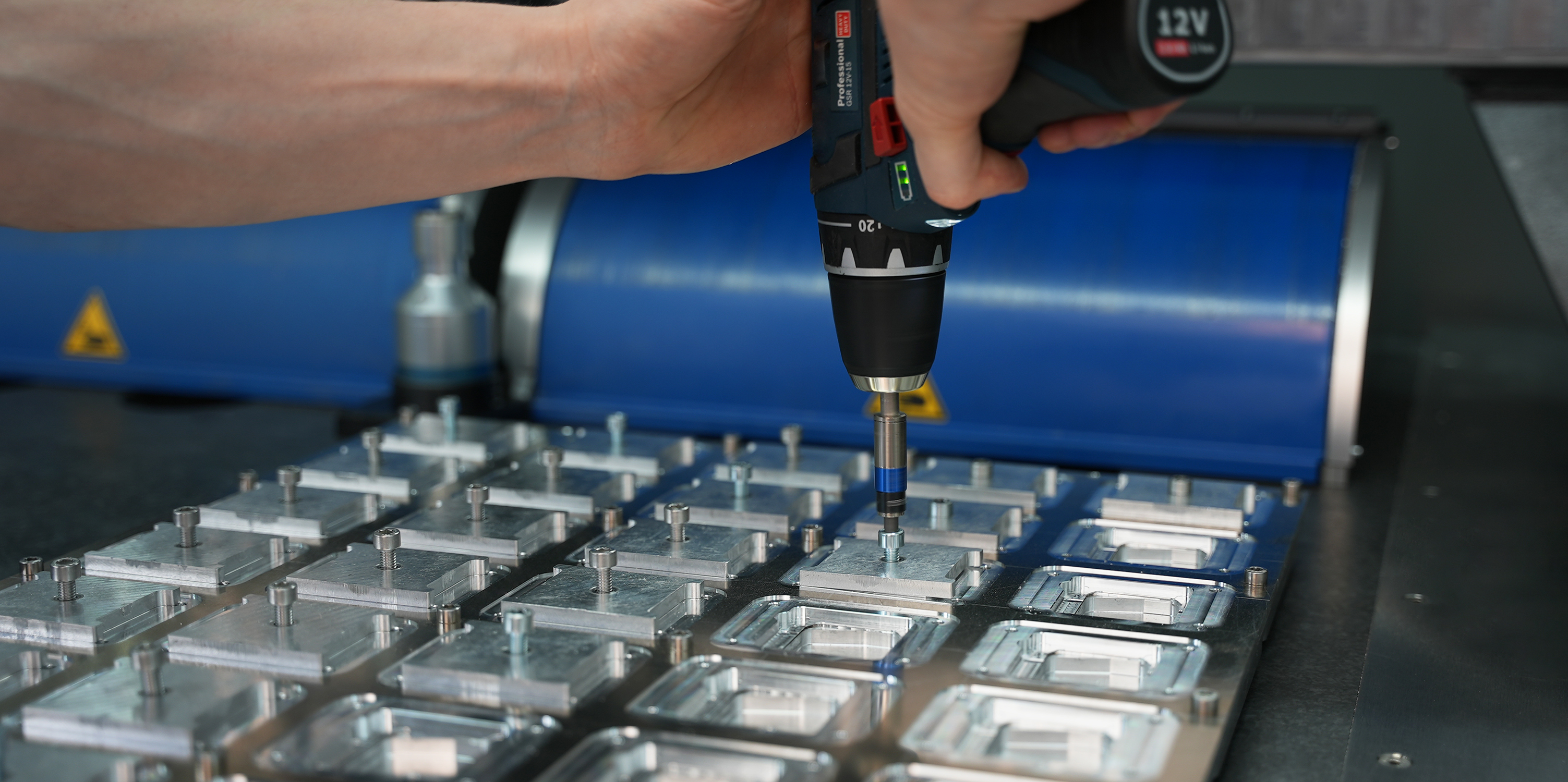
Quality control after milling
After milling, the direct-die frames are checked using a Keyence LMX multisensor measuring machine. The LMX can perform three types of high-precision measurements (±0.1 µm):
- high-precision image measurement
- non-contact height measurement using a multi-color laser
- tactile measurement using a 3D measuring probe.
Laser height measurement is used to measure the DDFs and 27 measurements are carried out per frame. In terms of the type of measurement, the LMX distinguishes between three different measurements in the case of DDFs. Of particular relevance here is the measurement of the relative height differences within the inner contour of the frame. The tolerances accepted during quality control are 0.05 to 0.5 millimeters, depending on the specified nominal dimension. The higher the nominal dimension, the higher the tolerance may be.
Once measuring on the Keyence LMX has been completed and all frames are OK, they are passed on for sandblasting.
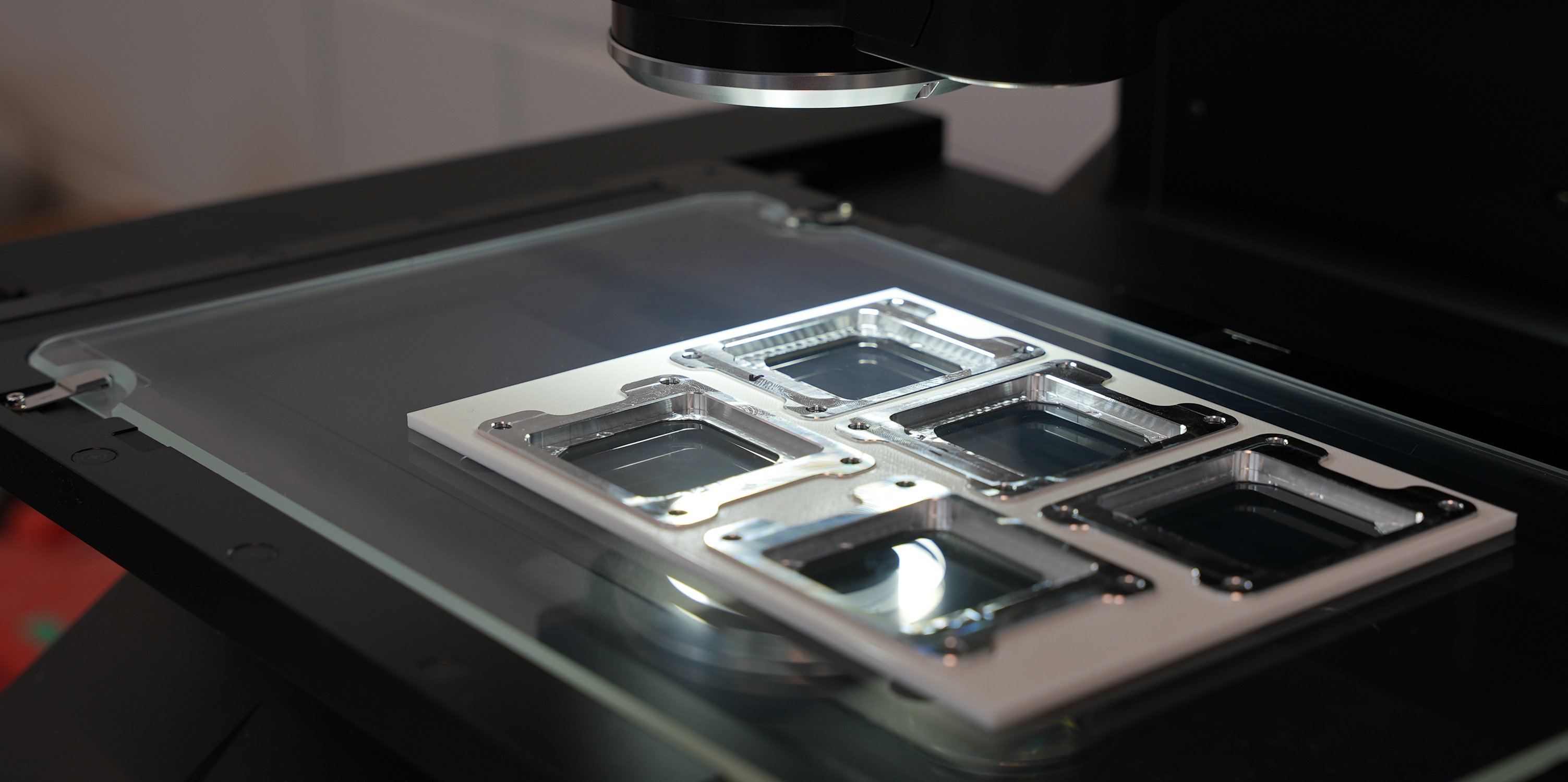
Sandblasting the Direct-Die-Frames
The next step after milling and quality control is sandblasting. This step is carried out in preparation for anodizing. Sandblasting with glass beads creates a uniform surface. Among other things, milling marks in the material are removed and residue from the milling machine's coolant is removed. The surface treatment by sandblasting helps to achieve uniform anodizing.
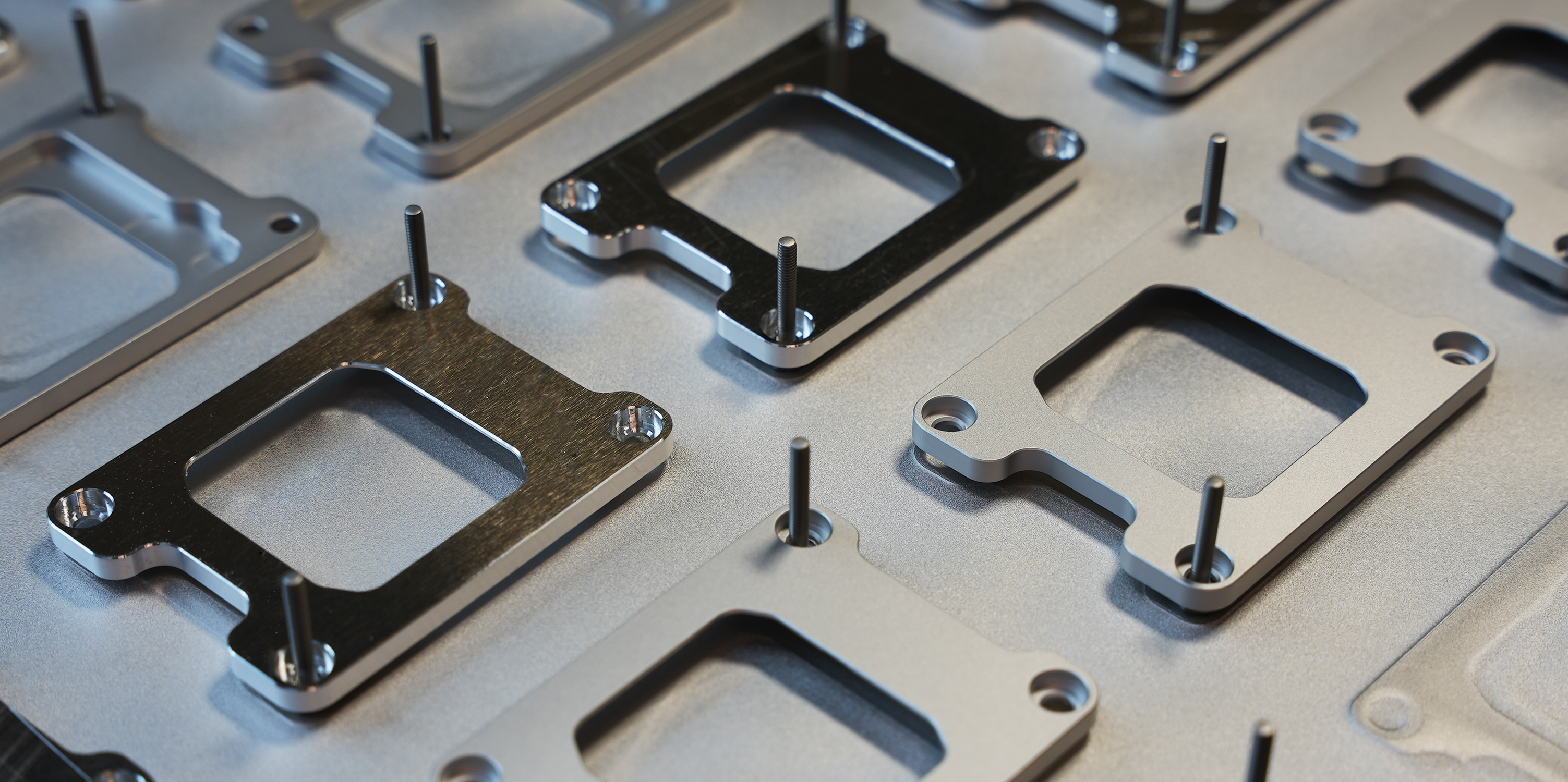
Quality control, external anodizing and engraving
After sandblasting, the direct-die frames are collected and prepared in large batches for dispatch for anodizing. This is also a further step in quality control, as all sandblasted direct-die frames with optical defects are sorted out. This process is also carried out manually by our trained staff.
Anodizing is an electrochemical process in which an artificial oxide layer is applied to the metal alloy. An aluminum workpiece is immersed in a water tank in which an electric current is circulated. During the electrolysis process, oxygen is combined with aluminum. Anodizing generally increases corrosion resistance, which includes protecting the aluminum from liquid metal. Without a protective layer such as that created during anodizing, the gallium contained in liquid metal would damage the aluminium through boundary layer diffusion. Diffusion is the physical process in which two substances mix.
When the DDFs come back from our external service provider for anodizing, the frames still have to be engraved by laser. For this purpose, the frames are placed in a specially manufactured holder and then engraved with a Trotec Speedy 360 flexx.
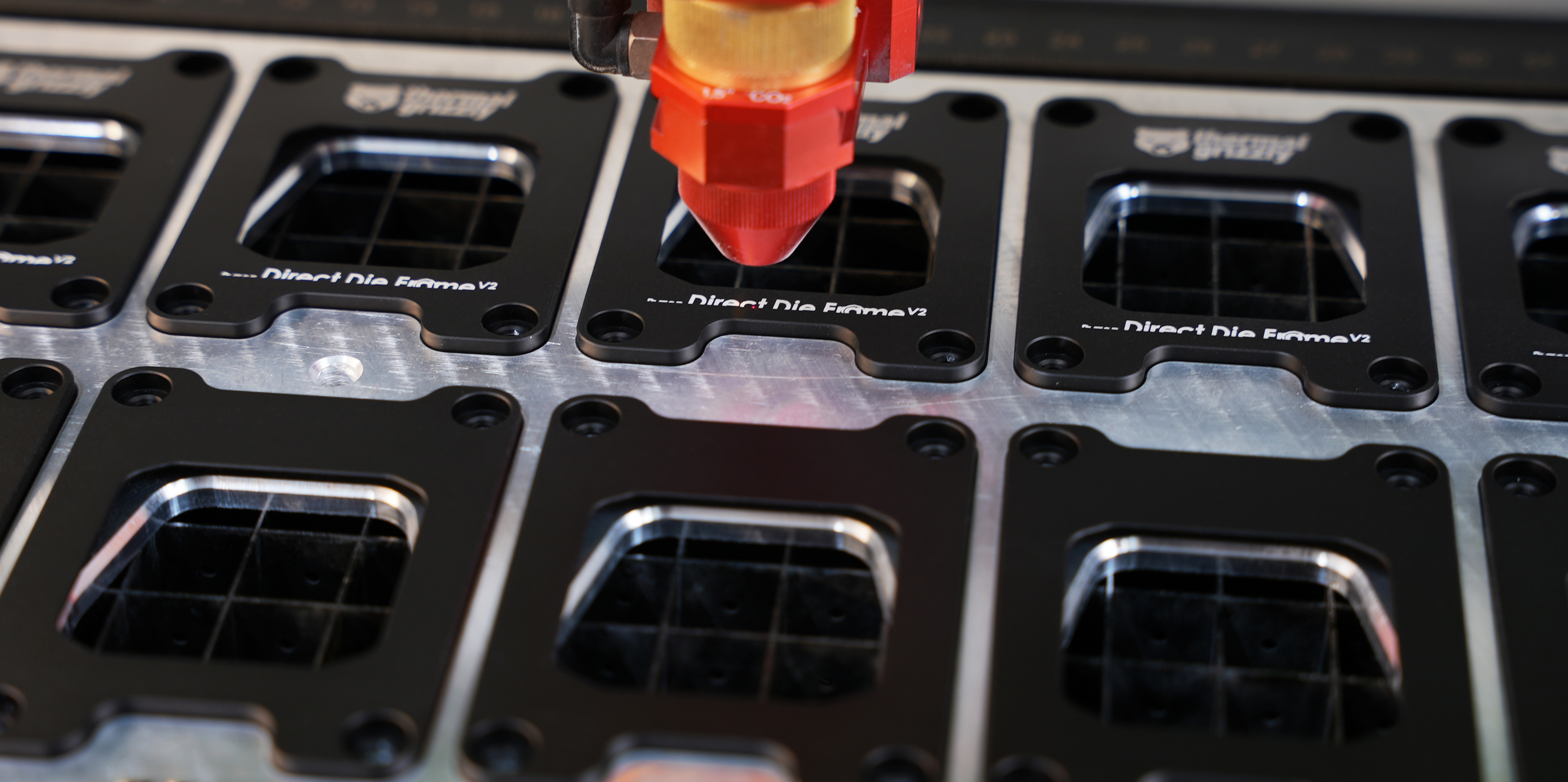
Last check and packaging
After engraving on the laser, the frames still need to be packaged. In this step, the direct-die frames are cleaned and checked one last time. Packaging takes place in three steps: The frame is placed in the cardboard box before it is placed in the bag with the rest of the packaging contents, which is sealed at the end. Before sealing, the packaged goods are checked for completeness using scales. Even the absence of a screw can be detected in this way.